Collaborative Research Centre 1153 "Process chain for the manufacture of hybrid high-performance components by tailored forming"
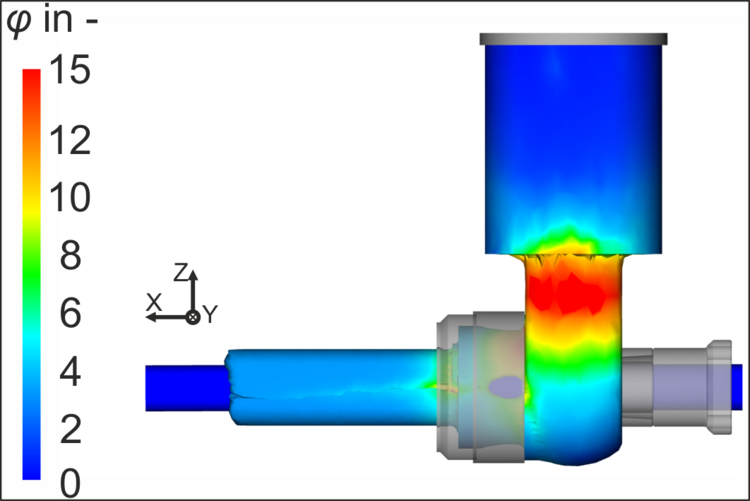
E-Mail: | fem@ifum.uni-hannover.de |
Year: | 2019 |
Funding: | German Research Foundation (DFG) - SFB 1153 TP A1 - Project number 252662854 |
Is Finished: | yes |
The aim of the second funding period is both to increase the lightweight potential of extruded concentric hybrid semi-finished products and to develop new hybrid semi-finished products with increased complexity and simultaneously high reinforcement content. To this end, the transferability of the developed Lateral Angular Co-Extrusion (LACE) process to other aluminium-titanium material combinations is being evaluated. On the other hand, the range of semi-finished products that can be produced by LACE is to be increased by using the knowledge gained about process control and die design to produce an asymmetrical demonstrator that is designed on the basis of a suspension control arm from the chassis area. A particular challenge here is the creation of a continuous, solid composite as well as dimensional accuracy due to the increased susceptibility to warpage, which occurs among other things as a result of the different coefficients of thermal expansion of aluminium and steel. The aluminium flow in the mould must be controlled in a reproducible manner to successfully bond the matrix material to the steel reinforcing component. A comprehensive numerical design of the process, which was already successfully implemented in the first funding period for the LACE process to produce concentric hybrid semi-finished products, is essential for the asymmetric demonstrator due to the significantly more demanding material flow. The resulting bond strength depends on the formation of intermetallic phases and their thickness. By using a diffusion-based approach the development of intermetallic phases can be numerical calculated under consideration of process dependent parameters like temperature, time or pressure.